Hard Foam Catalysts: A Comprehensive Overview
Introduction
Hard foam catalysts have emerged as a significant development in the field of chemical engineering and industrial applications. These unique materials combine the advantages of traditional catalysts with the benefits of a porous, lightweight structure, enabling efficient and sustainable chemical reactions. This essay aims to provide a comprehensive overview of hard foam catalysts, their preparation, properties, and applications.
Preparation of Hard Foam Catalysts
Hard foam catalysts are typically prepared using a foam-templating method. This process involves the creation of a foam, often from a polymeric material, which is then used as a template for the deposition or synthesis of the catalytic material. The foam is subsequently removed, leaving behind a porous, three-dimensional structure with high surface area and excellent mass transport properties.
The choice of foam material and catalyst precursor, as well as the conditions under which the deposition or synthesis occurs, can significantly influence the properties of the resulting hard foam catalyst. For instance, varying the pore size of the foam template can control the size and distribution of the catalytic material, while the use of different precursors can alter the chemical composition and activity of the catalyst.
Properties of Hard Foam Catalysts
Hard foam catalysts exhibit several advantageous properties that make them attractive for various applications. Their high surface area and porosity facilitate efficient contact between the catalyst and reactants, enhancing the rate and yield of chemical reactions. The three-dimensional structure of the catalyst also allows for excellent mass transport, reducing diffusion limitations and improving overall reaction efficiency.
Moreover, hard foam catalysts are typically lightweight and mechanically robust, making them easy to handle and suitable for use in large-scale industrial processes. They can also be designed to exhibit specific chemical properties, such as selectivity towards certain reactions or resistance to deactivation, by carefully controlling the synthesis conditions and choice of catalytic material.
Applications of Hard Foam Catalysts
Hard foam catalysts find applications in a wide range of industries, including chemical manufacturing, environmental remediation, and energy production. In chemical manufacturing, they can be used to catalyze various reactions, such as oxidation, reduction, and hydrogenation, with improved efficiency and selectivity compared to traditional catalysts.
In environmental remediation, hard foam catalysts can be used to degrade pollutants in air and water. Their high surface area and porosity make them effective at adsorbing pollutants, while their catalytic activity enables the degradation of these pollutants into harmless byproducts.
In the energy sector, hard foam catalysts are being explored for use in fuel cells and other energy conversion devices. Their unique structure and properties make them suitable for facilitating the electrochemical reactions that occur in these devices, potentially improving their efficiency and sustainability.
Conclusion
Hard foam catalysts represent a promising development in the field of catalysis, offering a combination of high surface area, porosity, and mechanical robustness that can enhance the efficiency and sustainability of various chemical processes. As our understanding of these materials continues to grow, it is expected that their use will become increasingly widespread, contributing to advancements in chemical manufacturing, environmental remediation, energy production, and beyond.
Recommended Reading:
N-Acetylmorpholine
N-Ethylmorpholine
Morpholine
High Quality 3164-85-* / K-15 Catalyst / Potassium Isooctanoate
High Quality Bismuth Octoate / 67874-71-* / Bismuth *-Ethylhexanoate
Bismuth *-Ethylhexanoate
Bismuth Octoate
High Quality BDMA / 103-83-* / Benzyldimethylamine / N,N-dimthylbenzylamine
Benzyldimethylamine
*-(*-Aminoethoxy)ethanol
DMAPA
Introduction
Hard foam catalysts have emerged as a significant development in the field of chemical engineering and industrial applications. These unique materials combine the advantages of traditional catalysts with the benefits of a porous, lightweight structure, enabling efficient and sustainable chemical reactions. This essay aims to provide a comprehensive overview of hard foam catalysts, their preparation, properties, and applications.
Preparation of Hard Foam Catalysts
Hard foam catalysts are typically prepared using a foam-templating method. This process involves the creation of a foam, often from a polymeric material, which is then used as a template for the deposition or synthesis of the catalytic material. The foam is subsequently removed, leaving behind a porous, three-dimensional structure with high surface area and excellent mass transport properties.
The choice of foam material and catalyst precursor, as well as the conditions under which the deposition or synthesis occurs, can significantly influence the properties of the resulting hard foam catalyst. For instance, varying the pore size of the foam template can control the size and distribution of the catalytic material, while the use of different precursors can alter the chemical composition and activity of the catalyst.
Properties of Hard Foam Catalysts
Hard foam catalysts exhibit several advantageous properties that make them attractive for various applications. Their high surface area and porosity facilitate efficient contact between the catalyst and reactants, enhancing the rate and yield of chemical reactions. The three-dimensional structure of the catalyst also allows for excellent mass transport, reducing diffusion limitations and improving overall reaction efficiency.
Moreover, hard foam catalysts are typically lightweight and mechanically robust, making them easy to handle and suitable for use in large-scale industrial processes. They can also be designed to exhibit specific chemical properties, such as selectivity towards certain reactions or resistance to deactivation, by carefully controlling the synthesis conditions and choice of catalytic material.
Applications of Hard Foam Catalysts
Hard foam catalysts find applications in a wide range of industries, including chemical manufacturing, environmental remediation, and energy production. In chemical manufacturing, they can be used to catalyze various reactions, such as oxidation, reduction, and hydrogenation, with improved efficiency and selectivity compared to traditional catalysts.
In environmental remediation, hard foam catalysts can be used to degrade pollutants in air and water. Their high surface area and porosity make them effective at adsorbing pollutants, while their catalytic activity enables the degradation of these pollutants into harmless byproducts.
In the energy sector, hard foam catalysts are being explored for use in fuel cells and other energy conversion devices. Their unique structure and properties make them suitable for facilitating the electrochemical reactions that occur in these devices, potentially improving their efficiency and sustainability.
Conclusion
Hard foam catalysts represent a promising development in the field of catalysis, offering a combination of high surface area, porosity, and mechanical robustness that can enhance the efficiency and sustainability of various chemical processes. As our understanding of these materials continues to grow, it is expected that their use will become increasingly widespread, contributing to advancements in chemical manufacturing, environmental remediation, energy production, and beyond.
Recommended Reading:
N-Acetylmorpholine
N-Ethylmorpholine
Morpholine
High Quality 3164-85-* / K-15 Catalyst / Potassium Isooctanoate
High Quality Bismuth Octoate / 67874-71-* / Bismuth *-Ethylhexanoate
Bismuth *-Ethylhexanoate
Bismuth Octoate
High Quality BDMA / 103-83-* / Benzyldimethylamine / N,N-dimthylbenzylamine
Benzyldimethylamine
*-(*-Aminoethoxy)ethanol
DMAPA
Hard Foam Catalysts: A Comprehensive Overview
Introduction
Hard foam catalysts have emerged as a significant development in the field of chemical engineering and industrial applications. These unique materials combine the advantages of traditional catalysts with the benefits of a porous, lightweight structure, enabling efficient and sustainable chemical reactions. This essay aims to provide a comprehensive overview of hard foam catalysts, their preparation, properties, and applications.
Preparation of Hard Foam Catalysts
Hard foam catalysts are typically prepared using a foam-templating method. This process involves the creation of a foam, often from a polymeric material, which is then used as a template for the deposition or synthesis of the catalytic material. The foam is subsequently removed, leaving behind a porous, three-dimensional structure with high surface area and excellent mass transport properties.
The choice of foam material and catalyst precursor, as well as the conditions under which the deposition or synthesis occurs, can significantly influence the properties of the resulting hard foam catalyst. For instance, varying the pore size of the foam template can control the size and distribution of the catalytic material, while the use of different precursors can alter the chemical composition and activity of the catalyst.
Properties of Hard Foam Catalysts
Hard foam catalysts exhibit several advantageous properties that make them attractive for various applications. Their high surface area and porosity facilitate efficient contact between the catalyst and reactants, enhancing the rate and yield of chemical reactions. The three-dimensional structure of the catalyst also allows for excellent mass transport, reducing diffusion limitations and improving overall reaction efficiency.
Moreover, hard foam catalysts are typically lightweight and mechanically robust, making them easy to handle and suitable for use in large-scale industrial processes. They can also be designed to exhibit specific chemical properties, such as selectivity towards certain reactions or resistance to deactivation, by carefully controlling the synthesis conditions and choice of catalytic material.
Applications of Hard Foam Catalysts
Hard foam catalysts find applications in a wide range of industries, including chemical manufacturing, environmental remediation, and energy production. In chemical manufacturing, they can be used to catalyze various reactions, such as oxidation, reduction, and hydrogenation, with improved efficiency and selectivity compared to traditional catalysts.
In environmental remediation, hard foam catalysts can be used to degrade pollutants in air and water. Their high surface area and porosity make them effective at adsorbing pollutants, while their catalytic activity enables the degradation of these pollutants into harmless byproducts.
In the energy sector, hard foam catalysts are being explored for use in fuel cells and other energy conversion devices. Their unique structure and properties make them suitable for facilitating the electrochemical reactions that occur in these devices, potentially improving their efficiency and sustainability.
Conclusion
Hard foam catalysts represent a promising development in the field of catalysis, offering a combination of high surface area, porosity, and mechanical robustness that can enhance the efficiency and sustainability of various chemical processes. As our understanding of these materials continues to grow, it is expected that their use will become increasingly widespread, contributing to advancements in chemical manufacturing, environmental remediation, energy production, and beyond.
Recommended Reading:
N-Acetylmorpholine
N-Ethylmorpholine
Morpholine
High Quality 3164-85-0 / K-15 Catalyst / Potassium Isooctanoate
High Quality Bismuth Octoate / 67874-71-9 / Bismuth 2-Ethylhexanoate
Bismuth 2-Ethylhexanoate
Bismuth Octoate
High Quality BDMA / 103-83-3 / Benzyldimethylamine / N,N-dimthylbenzylamine
Benzyldimethylamine
2-(2-Aminoethoxy)ethanol
DMAPA
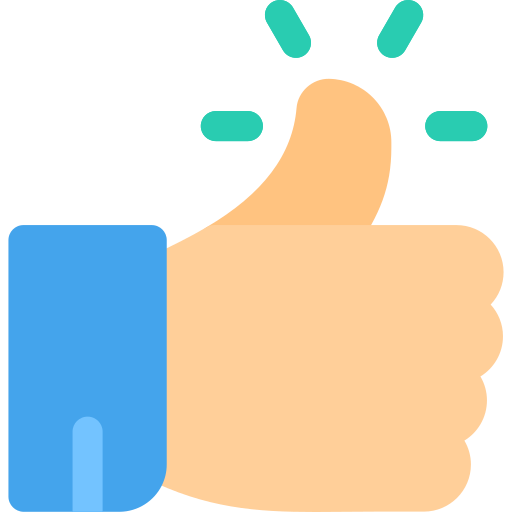